Tungsten Copper Button Contact
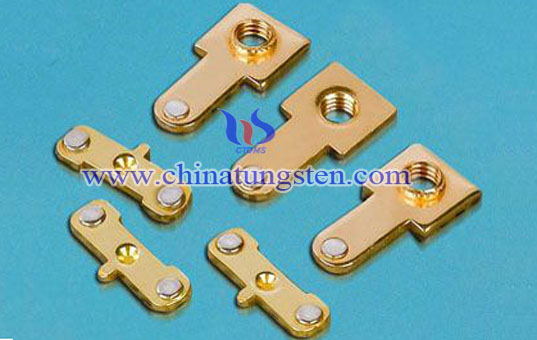
מבוא
Tungsten copper button contact is main parts for high-voltage circuit breakers, switchgear, disconnections and grounding switch. In the high-pressure, high pressure SF6 circuit breaker system, the arc contact currently used to CuW based alloy, moving past the arc contact arcing contacts are finger - spring structure, which complicated the work of the spring heat, its reliability is deteriorated.
Tungsten copper button contact in appliances bear making, carrying and breaking normal current and fault current function, it requires low contact resistance and reliability, long life and so on. Since the electrical conditions vary greatly, therefore, on the contact material presented diverse performance requirements. But for a variety of performance requirements, none of the contact material can be fully satisfied, it must be selected according to the different characteristics of various materials.
מעבד
Infiltration
Infiltration first to tungsten powder or molybdenum powder pressing and sintering into tungsten, molybdenum skeleton has a certain porosity, infiltration and copper. This method is suitable for low copper content of copper tungsten, molybdenum, copper products.
Copper Oxide Method
Copper oxide is prepared by mixing and grinding method to extract copper reduction, rather than directly with the metal copper powder, copper continuous matrix is formed in the sintered compacts, tungsten as strengthening the framework. High expansion component of the second component is subject to four weeks, powder sintering at lower temperature wet hydrogen.
Injection Molding
Injection molding is a relatively common method of making tungsten-copper alloy. Tungsten copper alloy contacts injection molding is uniform particle size of 1-5 microns nickel powder, tungsten powder, copper or iron with a particle size of 0.5 micron tungsten powder and tungsten powder mixing 5-15 microns, Remixed into the 25% -30% of an organic binder agent (such as paraffin or polymethyl methacrylate vinegar) injection molding, steam cleaning and irradiation in addition to the binder, sintering in hydrogen, to obtain a high-density tungsten-copper alloy.
Development Status
With the rapid development of modern industry, industrial electrical control, increasing the level of intelligence, increasing high voltage transmission network load, low-voltage power distribution and control systems as well as the continuous development of the electronics industry update replacement products. Electrical products to large capacity, small size and direction, along with electrical products for heart device - electrical contact material put forward higher demands to the material under tremendous heat and arcing Joule heat, the melting does not occur good welding, mechanical wear and abrasion resistance, electrical properties; metal produced in the process of breaking splashes should not be excessive, arcing time not too long; in the current environment, good welding resistance, low and stable contact resistance.
Around the national key pillar industry in the future will develop multi-family, high-performance electrical alloy products. Electrical contact materials will be increasingly automated production lines, further to the element of direction, the development of advanced, practical and efficient special tooling equipment, improve reliability, stability, corrosion resistance and other properties of the product.