Tungsten Copper SPS
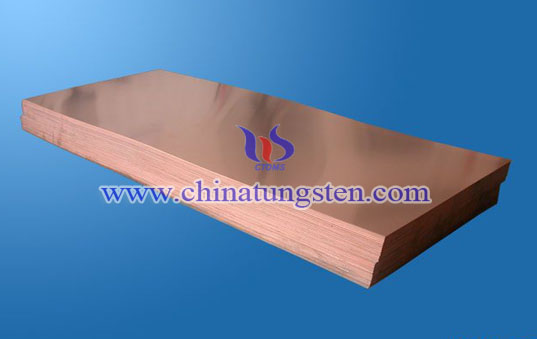
Introduction
Spark Plasma Sintering (SPS) is a kind of new sintering technology based on electrical discharge machining. It belongs to plasma sintering technology, which uses sparks and gap discharge to sinter in pressure. While the other is in a vacuum environment, uses 5000-20000k plasma flame to heat sintering, this called thermal plasma sintering.
Process
The basic principle of SPS is that use the instantaneous high temperature produced by pulse energy, pulse discharge pressure and the Joule heat to achieve sintering process and by instantly generate a plasma discharge inside each particle is sintered to produce a homogeneous particle surface activation and self-heating. Furthermore, SPS process can be widely used in ceramics, cermet, Intermetallic compound, FGM (Functional gradient Material), thermoelectric materials, ferroelectric materials, magnetic materials, nano materials, amorphous alloys fabricating. In brief, SPS process is to inlet pulse current directly into the powder grains for heat sintering, so it always called as plasma activated sintering or Ion-assisted sintering technology.
Advantages
Compared with conventional vacuum sintering process, SPS process has many advantages in nano tungsten carbide machining, such as finer granularity, higher densification, more uniform structure and no apparent porosity defects. In the process of SPS sintering, the densification of the samples will never decrease when the temperature exceeds an optimum value. This is due to the volatile Co does not appear in the SPS phase sintering process, the sample has been densified with sintering temperature increases; from the view of hardness, Rockwell hardness and micro hardness of sample after the sintering SPS are significantly higher than traditional vacuum sintering samples.