Tungsten Copper Metal Injection Molding
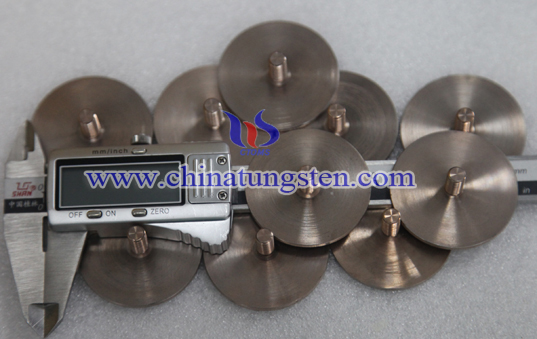
Introduction
Tungsten copper metal injection molding (MIM) is a new type of powder forming technology, which also called powder injection molding (PIM), it is a method combines by powder metallurgy and injection molding. Which is with two main ways: One is only the W powder injection molding made of tungsten skeleton, the other is the W-Cu mixed powder by injection molding. Blank prepared two ways need degreasing treatment, densification and other technology. Foreign scholars prepared by injection molding technology combined with tungsten skeleton infiltrated prepared by the excellent performance of tungsten copper products.
Advantages
Tungsten copper metal injection molding method is a new powder metallurgy net shape technology in the manufacture of complex geometries having a uniform structure and high performance, low cost and high precision net shape and so has a unique advantage, and can be fully automated continuous operation, high production efficiency. Studies have shown that the metal injection molding process to produce small size, complex shape W-Cu net shaped product, is economical and effective. Performance powder are the main factors affecting the MIM process, requiring very fine raw material powder (about 10un), nearly spherical particles, large specific surface energy, in order to ensure the dispersion of powder flowability is higher, larger firing rate.
Disadvantages
Tungsten copper metal injection molding method and the infiltration method combining deficiencies at specific performance in: after infiltration need to be machined to remove excess copper, an increase of subsequent machining costs, higher process cost, process complexity, reduce the yield, and not conducive to the use of the complex shape of the parts.