Tungsten Copper Fiber Structured Contact
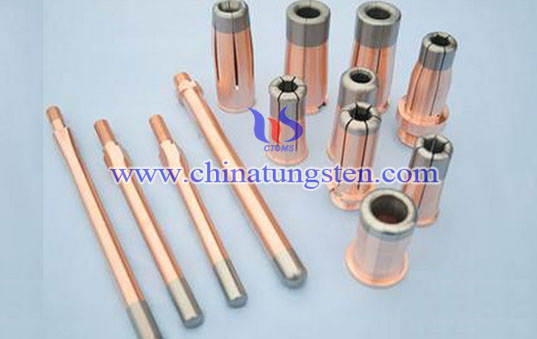
Introduction
Being a pseudo-two-phase alloy composed of Cu and W elements, tungsten copper composites have not only high melting point, high density, low thermal coefficient of expansion and high strength, but also better electric conduction, better heat conduction and plasticity under room temperature. Thus tungsten copper composites are applied extensively as electrical contact material and electrode materials. In the late 1980s, tungsten copper alloy was used widely, such as contact material of vacuum circuit breaker, substrates of large-scale IC (integrate circuit) and high-powder microwave apparatus, seal and package materials and joint parts and radiator apparatus. It is required that tungsten copper composites which are used as contact materials of vacuum circuit breaker and electron appliances should possess the properties of high-density, low gas-leaking, better electric conduction and heat conduction. While conventional tungsten copper alloy are manufactured in the power metallurgy technique which require high quality of tungsten powder and copper power.
As for the present technology, the produced tungsten power and copper power contain high amount of gas, which limit electrical contact performance. For example, the density of contact materials is quite low (because contact materials manufactured in powder metallurgy technique are easily inflatable during the course of sintering, yet it is difficult to sinter densely. The best density can attain 92%~95%), the gas content is high, and electrical and thermal conductivity is low. In order to overcome disfigurement of conventional techniques and meet the requirement for contact materials of vacuum circuit breaker and micro-electron industry, our scientific group research and develop a kind of new preparation technique of tungsten copper composites-fiber structured strengthen tungsten copper composite.
Processing
Tungsten as the weft, copper wire as warp knit two-dimensional network, put stacked together the network and copper billets, and prepared by infiltration process sintering in vacuum furnace. Sintering above the melting point of copper, the temperature is about 1300℃, copper in the molten state, through capillary action to fill in the pores of tungsten framework, and then formed integrally material kinds of a dense and connected to each other.
Advantages
1. Tungsten fiber and strengthen copper matrix technique is applied for the first time to make electrical contact materials and achieves its laboratory experiment. Infiltration techniques are adopted in tungsten copper composites' shape sintering, and the material's relative density is bigger than 99%. While compared with the best relative density of power metallurgical contact material is 92%~95%. The former is higher than the latter.
2. In the same condition, the surface of fiber-structured and the surface of power metallurgical contact materials received experiment with electrical are erosion by argon arc welding torch. And we analyze its surface appearance. Result shows that ablation of fiber-structured contact materials is better than that of power metallurgical ones and ablation of small diameter fiber-structured contact materials are superior to that of large diameter ones.