Tungsten Copper SAW Contact Tips
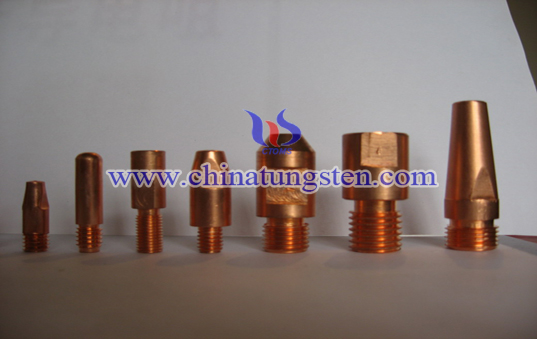
Introduction
Tungsten copper SAW (Submerged arc welding) contact tips are the welding comsumables, which usually located at the end of welding equipment and plays an important role in welding wire conducting.
Characteristics
Tungsten copper SAW contact tips use arc as the heat source, the arc burns at meltable particulate flux covered, not exposed, so called SAW. It has many advantages, such as good welding stability, high welding efficiency, good welding quality, no arc light and less smoke, which is a main welding process in pressure vessels, pipe manufacturing and box beams (such as boilers, shipbuilding, bridge construction, heavy machinery, construction of nuclear power plants, weapons manufacturing, etc.) and other important steel manufacturing. And it has a wide range of suitable welding materials, includes carbon structural steel, low alloy steel, stainless steel and some non-ferrous metals, such as copper-based alloys, titanium and nickel-based alloys.
Comparison
In the process of SAW process, due to the large current and electric field strength of the arc is relativey high, the contact tip materials that require more than just good thermal conductivity properties, but also the need for better hardness, strength resistance arc erosion ability. Currently, most of industries use copper or chromium zirconium copper as SAW contact tip, which has poor wear resistance and prone to block the tips caused by adhesion and splashing, or the welding wire and contact tips will be bonded and resulting in the failure of contact tips. In addition, in some important occasions, usually due to the wear, frequent replacement of the contact tips affects the welding quality and reduces the overall productivity. Tungsten copper and aluminua copper contact tip even under high current environment is still able to maintain excellent performance, it has a strong anti-arc erosion ability, thus longer service life, reducing replacement frequency, improve SAW efficiency.